ERP: created by visual programing, can be custom developed according to specific requirements
MES: for manufacturing or other business task/order management, detailed process and related data management
ERP + MES + more…
ERP+MES Management System with Custom Development Service
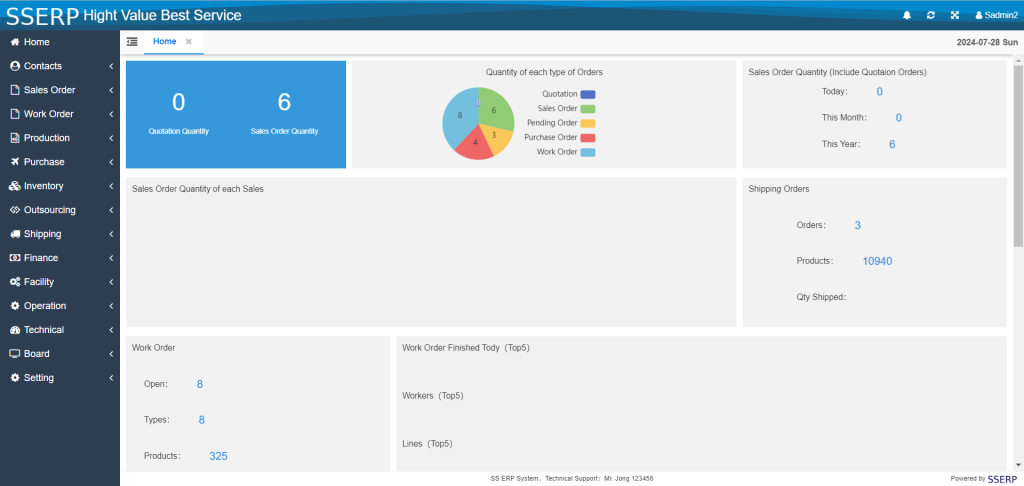
Advantages Compared with other ERP+MES system
- Basic modules finished for ERP and MES, suitable for manufacturing, project task management, multiple works / job management
- Can be upgrade according to customers request, update again and again, don’t wrong about different developers works, all are same because all developers use same elements
- Custom design based on finished pages or modules, save time and cost
- With this application we can provide demo project in 72 hours to verify the application, lower risk for customer
- Customer can buy the project and maintain or upgrade by own developers, more control and more cost saved for the long term
Contact us for tool, solution, standard software and custom develop sevice
Feature List of Standard ERP+MES system
# | Module | Feature | Details |
1.1 | Customer/Supplier management | Company/Supplier Information CRUD | Contact Info, Tracking information, Multi Contacts, Multi Receivers, Types, Credit limit for shipping, Date number of issue invoice etc. |
1.2 | CRM function | Contact Info, track the progress of contacted details each time finished | |
2.1 | Sales Orders management | Quotation Order | Just a quotation order, need to check with customer and change to Sales order if approved, track progress with customers, check inventory available |
2.2 | Sales Order | Can be proceed with shipping or production work orders | |
2.3 | Inventory Check | When the product identified, check current inventory | |
2.4 | Price Book | Automatically check price for this customer and same product other customer prices | |
2.5 | Production Arrangement | Arrange quantity to produce later | |
2.6 | Contract Generate from Template | If a template there is, will generate a contract for print or send or post | |
2.7 | Files | Store Customer Quotation, Product files, Contract Files | |
2.8 | Shipping advises | If have inventory or come to date for shipping, arrange the quantity to delivery | |
2.9 | Tracking functions | Quantity, Amount, Quantity Shipped, Amount received, other cost etc. | |
3.1 | Planning & Work Order | Planning | According to inventory or sales order quantity, run MRP to generate material purchase request, or generate work order of each type of products, those are prepared for the final product work orders, same products can be combined for planning, plan is generated by BOMs of each product |
3.2 | Work Order | Can be generated by sales order or create it manually according to current inventory, arrange the process of manufacturing, track the progress automatically if the result is submitted according to work order, print all kinds of labels such as transfer labels OQA labels etc. | |
4.1 | Manufacturing Management | Reports | Quantity report, tracking report, process alert if not meet target, delayed orders check and tracking |
4.2 | Performance Management | Quality, on time complete, delay etc. | |
5.1 | Purchase Order | Request Management | Check requests, arrange suppliers and prices, quantity can be updated, receive date management and feedback to sales |
5.2 | Order Create | By check items and assign supplier, generate purchase order automatically with a template prepared, print or send or post according to work process | |
5.3 | Purchase Parts Receiving | Different patch, lot, date with each part, confirm the price or calculate cost along with receiving | |
5.4 | Purchase types | Purchase according to sales orders or purchase combined quantities, purchase by orders can be a lean process save time | |
5.5 | Tracking and management | Tracking payment amount according to orders, quantity received or rejected, other cost such as fee | |
5.6 | Files | Purchase contract, purchase orders, invoice etc. | |
6.1 | Warehouse Inventory | Product data | Name, specification, photo, files, color, purchase or manufacturing types, labels etc. |
6.2 | Inventory | Check on time real inventory, same part in different warehouse etc. | |
6.3 | Material In Out Details | Register in and out, automatically in out records, material or products transfer from warehouse to others, check details of all types of transactions | |
6.4 | Tracking | Register lot number, date, and instruct quantity of lots according to FIFA policy | |
7.1 | Shipping | Shipping advises | In sales order sales can check inventory of each open order and all product inventory, set shipping quantity and confirm as advise |
7.2 | Delivery arrangement | Arrange items to be shipped together and generate shipping list automatically according to designed template, print packing labels or other documents | |
7.3 | Delivery data | Delivery order number, truck, third party shipping data (express) etc feedback to sales automatically | |
8.1 | Invoice and Payment | Invoice for customer | Can be generated according to weekly shipping date or each delivery, printed or download and send or post |
8.2 | Shipping Details | Both purchase parts, outsourced parts, for each supplier generate receive list and pay by this data; for shipping parts of each customer, also a shipping details list or report of multi shipping data is available | |
8.3 | Payment from customer | Register payment amount and date, automatically calculate remains of shipping parts | |
8.4 | Payment for supplier | Register payment amount and date, automatically calculate remains of purchase parts outsourced parts | |
9 | IEquipment Management | Equipment, tools, facilities management | Name, status, owner, check time, validation time, all kinds of photo and other files etc. |
10 | Operations Records | Check and maintain actions recorded | Actions recorded |
11.1 | Outsourcing | Outsourcing | Request from work order, set supplier and price, receive when finished |
11.2 | Tracking | Tracking Material delivered to outsourcing suppliers, current inventory, status of each part and quantity received and remained, other cost register | |
12 | Setting for Production | Process, BOM | Product process, BOM etc. |
13.1 | Visual Management Board | Data on Board | Order data, sales data, work order progress data |
13.2 | Show Types | Charts, colorful table data etc. | |
13.3 | Refresh | Refresh based on a set interval such as 10 seconds | |
14 | Front Page Summary Data | Total amount or quantity or finished or other data | Total amount or quantity or finished or other data can be shown on front page to support management. |
15.1 | System Setting | User Management | User Account user information etc. |
15.2 | Authorization Management | Roles, Permissions | |
16 | Mobile Devices | Scan QR code bar code with PDA | To check inventory, order details, product details, move material, FIFA data etc. |
Contact us for tool, solution, standard software and custom develop sevice